Managing ink is an important consideration when starting any color profiling project for inkjet devices. Requirements for dry or cure time and adhesion are based on customer’s post-production and end-product use. In our last article in the Color Management series, we addressed banding issues and how they affect color profiling, now let’s discuss the aspects of drying that should be understood before starting any color profiling process.
Drying/Curing
Aqueous inks are dried and UV inks are cured through the application of heat or energy. These processes remove moisture, in the case of drying, or create a molecular change to the ink chemistry, in the case of curing. Proper drying and curing promote good rub and abrasion resistance. The process differs by ink type and also by substrate type. In addition, printer speed, jetting speed, drop volume and surface tension between the ink and substrate affect proper drying/curing settings.
- Non-porous substrates require different attention than porous because the ink reacts within milliseconds on the substrate surface.
- Non-porous substrates require controlled wet-out to avoid defects such as color to color bleed, edge wicking and coalescence (as the ink wets out or has too much time before drying/curing occurs). These defects can result in uneven surface color leaving dark and light blotchiness.
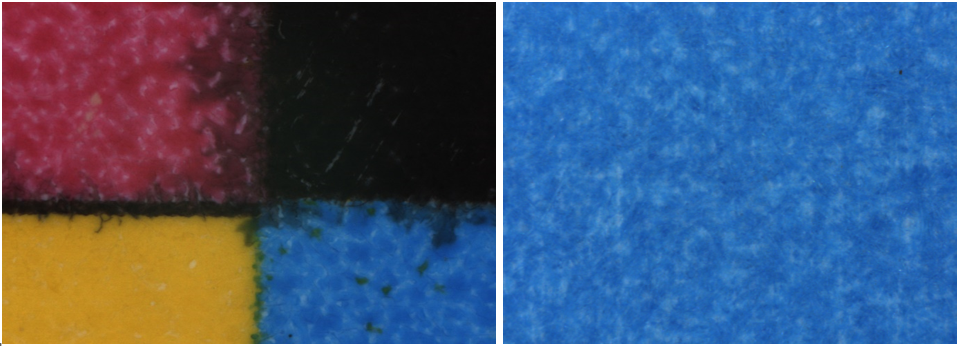
Color to Color Bleed Coalescence
On the other hand, intensive settings can dry or cure too quickly leaving the ink with surface cure, but an internal ink base that is uncured. This creates an effect, where the ink dry to the touch but will roll up when resistance is applied, known as improper adhesion.
Adhesion
Ink must adhere or stick to the substrate through-out production and beyond; from manufacturing to final handling the product. If adhesion fails, manufacturers and consumers will see the product ,as well as the inkjet process, as a failure. Applying color management or ink limiting will not address adhesion issues but should be reviewed as part of the ink management process.
Many considerations such as drying (improper primary ink cure), excessive combined ink thickness (high TAC) or targeting improper color spaces can leave the ink thick enough to result in the visible issues mentioned above and also affect proper adhesion of the ink to the substrate. To make managing the process easier to understand, remember the SAFE method.
- Surface – Understand surface chemistry – paper (types), plastic, metal, fabric, glass
- Application – Outline the print process – ink, speed, heat, air, IR, UV, single pass, XY
- Finishing – Define post processes – cut, stack, insert, fold, chemical bath, coating, laser
- End Handling – Review all requirements – mailed, fill-line, stacked, packaged, shipped, cold or hot filled, refrigerated, general or abrasive handling.
Outlining the print and ink requirements is the first step in determining how color profiles will be created and ink limits addressed. Determine what will be printed, how it will be printed, impact of post printing and final handling requirements. Understand the material and the process as it relates to the printer, ink and substrate interaction as well as the methods needed to adjust and test the final product. Look at the entire process, not just color.
If the ink does not stick to the substrate, it is unlikely it will meet the customer’s requirements. Adhesion should be tested at the primary color level using the ASTM D3359 method at different speeds and drying/curing settings before color management. Developed by the American Society for Testing and Materials this simple test uses a test cross hatch pattern and very sticky tape. Surprisingly though, this testing is rarely completed before ink limit is determined for the profile.
Print defects are normally not caused by just one thing. Even though process color inks are supplied with a particular device, pL volume and wet out of one or 2 colors combined can change their reaction with the substrate. Ink to ink compatibility is determined by reviewing the ink’s wet-out or flow characteristics, adjusting drop volume and single ink thickness.
Inconsistent surface tension and temperature surfaces are also large contributor to the issues mentioned above. Pretreatments such as coatings, flame, corona, or plasma can be applied to assist with ink to surface compatibility. Each one having its own set of challenges and not easily added without extensive testing and process re-engineering.
Any ink to substrate issues must be addressed by focusing on the source of the print defect by addressing which ink (or inks) are not compatible with each other or the substrate; and where in the individual ink coverage this is occurring. Again, looking at how the pieces get along before trying to color manage the process.
Whether you are printing for commercial or industrial, or in-line or off-line manufacturing, the process of color management is an important one and should be addressed to provide the proper brand consistency. But only once all the pieces of the process have been outlined with a full understanding of ink to substrate compatibility. Only by understanding all the pieces can you manage your color without process conflict.
If this process sounds complex, it is. That is why color consultants with overall knowledge of the process and experience with different presses and substrates are in such high demand. We offer these posts to help you understand and master the process, but if you would rather have someone manage the process for you, or provide more extensive keep us in mind.
Want to learn even more about the impact of drying? Check out our recent Explainer Webinar: Understanding Inkjet Drying Technology.