Designing a single pass inkjet system from scratch to meet the demands of requirements in the production inkjet market is not an easy task. Development of industrial flat or in-the-round bespoke systems designed to be integrated into a manufacturing process takes even more homework. Inkjet printing is being added into the manufacturing process:
- By printing directly after the part as extruded or formed in line with manufacturing
- Or after the part formation process
Plastics, glass, ceramics, laminates, metals, and fiber substrates are being printed using inkjet in line with manufacturing. This requires a complete understanding of, not just the print head and drive requirements but, the environment to which the inkjet system will be exposed, and the condition of the part being printed.
Inkjet integrators don’t begin their design process with printheads as one would think but start with the many other considerations which affect print quality. When developing a new inkjet press, or creating a custom integration, top print results don’t happen by accident. Let’s look at what can affect print quality and what should be considered for every development project. We’ll start with understanding important customer requirements and the homework the integrator must complete.
Print/Market Requirements
First, we must take into account the customer’s reasoning for integrating custom inkjet rather than seeking a commercially available solution. The customer’s requirements for print and color quality depend on which market they operate in. Not all markets require graphic arts quality. Flooring, for example requires a much different design scope than custom beer cans. Both need to be appealing to the consumer, but flooring requires different levels of image quality.
Flooring devices generally use UV ink chemistry for surface abrasion, printed with 2-3 spot colors (n-colors) plus varnish, and a large (18pl and higher) binary drop. Designed for a more aggressive manufacturing/single pass print environment. For contrast, custom cans often are printed in the round using UV ink jetted with smaller drop sizes (3-12pl) utilizing multi-level drop sizes, CMYK+spot/varnish. The process is generally integrated offline from manufacturing offering a cleaner production environment. When designing bespoke inkjet solutions, 3 baseline considerations determine the level of image and color quality required.
- Viewing distance of the end product
- Expectations color and image detail such as: small text legibility, image quality, solid coverage, brand color matching sensitivity
- Market requirements e.g. the product will be displayed or the need to match other print processes
- Environmental use and exposure e.g. abrasion, moisture and flexibility requirements
Print Quality Forms the Foundation of Color Quality
Since proper ink laydown is the literal foundation for print and color quality. Its impact on quality can be seen in different forms:
- Jet errors
- Grainy images
- Rowing
- Color uniformity
- Head banding
- Solid mottle/coalescence
- Artifacts
- Satellite drops
- Low Resolution
- Edge clarity
- Line clarity
- Color to color bleed
- Registration
As the bespoke design conversations start, the entire process must focus on ensuring that all quality requirements are met throughout the process – these issues are difficult, if not impossible to correct in the 11th hour.
Many people think you can color manage anything at the back end to get the result you want. You can’t. You have to have the proper foundation to work with or you are reverse engineering your project at the end not “color managing.”
With Inkjet Development Everything Affects Everything
Crazy as it may seem, each of the bubbles below could be expanded out more than 20 times to show additional levels of complexity that must be managed. For now, let’s keep looking at the process for designing a bespoke system from a few thousand feet up.
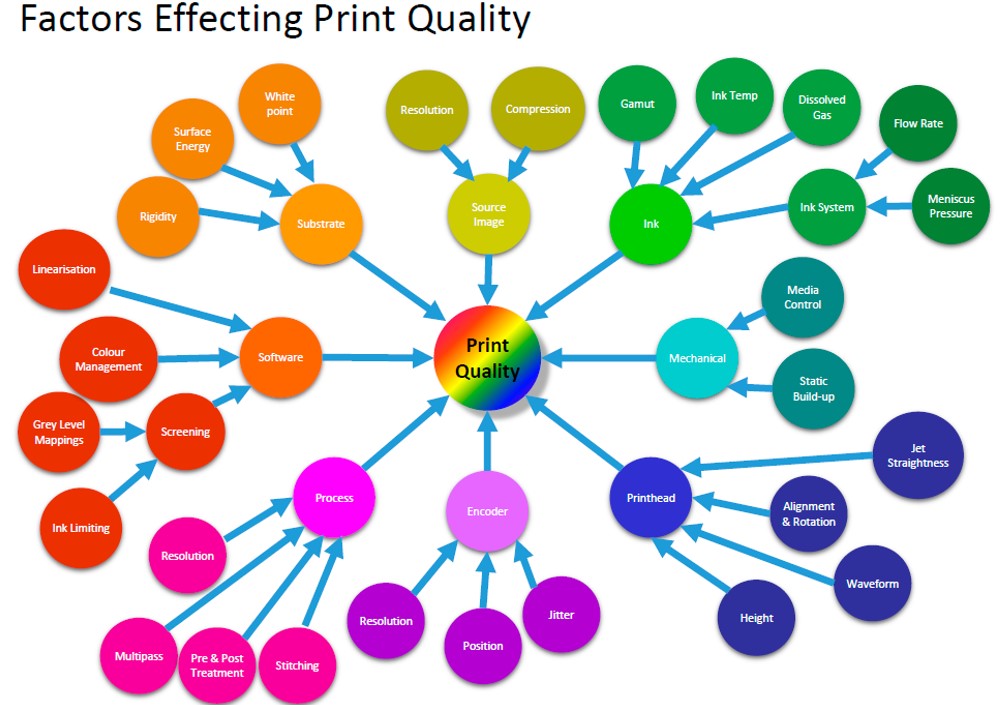
Chart supplied by Global Inkjet Systems.
Substrate/Ink
Ink suitable for the target substrates is the first consideration in any inkjet system design once requirements have been established. Substrate and ink go hand-in-hand. Proper ink laydown is critical to print and color quality and the consistency of ink laydown is determined by the substrate’s compatibility with ink. The substrate surface and chemistry are designed to operate within a specific surface tension range.
When starting any inkjet integration project, integrators start with ink chemistry and define ink characteristics to ensure proper wet-out and adhesion through adjusting chemistry and surface tension. If the ink is designed for a specific substrate surface tension, a vendor change of substrate with surface differences can create ink compatibility issues.
Unfortunately, ink wetting and adhesion will vary from material to material and ink to ink, so printing a wide range of products or various suppliers with one ink/process should be addressed at the start of the development phase.
Inkjet wet-out differences
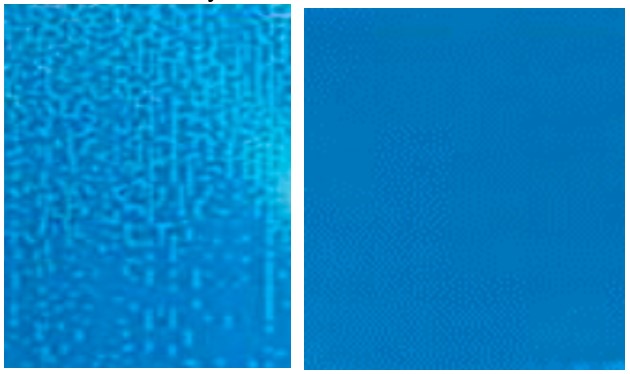
Ink surface tension issues Pretreatment applied
Ink and surface compatibility factors can also determine if an in-line or off-line pretreatment is required, which can add additional complexity and cost to the project.
Examples of Pretreatments:
- Alcohol
- Flame
- Corona
- Plasma
- Primer- jetted or anilox
Each treatment type is dependent on the process, target substrate, and ink with different resulting cost and integration considerations. Each supplier’s version of the pretreatment will also vary.
Environment
Just as important as knowing the composition of the substrate are the environmental factors which the substrate must endure. Ink and surface chemistry is based on a narrow tolerance window and changes in the surrounding environment can affect the ink laydown, and therefore print quality.
- Chemistry composition
- Humidity
- Ambient temperature changes
- Temperature of substrate
- Dust
- Dirt/fingerprints
The print production environment should be closely understood and mimicked in development to determine environmental tolerance ranges for final production installations. If components are evaluated separately, the heating or particle impact of one component on another may not be noted soon enough in the process.
Motion Control/Handling
Now that the substrate, ink, and the environment are understood, let’s look at material handling and production requirements that can affect print quality. The customer most likely has a good idea on the number of parts they wish to print per hour. This factor determines:
- Print width
- Scan type (carriage or single pass)
- Print direction
- Number of print heads required
- Encoder
- Part automation/handling
- Length of print unit/
Material handling can include existing motion control with which the inkjet process must integrate, or a design custom.
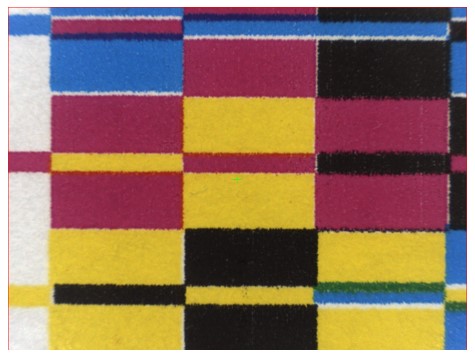
Image shows color to color registration mis-aligned from inaccurate reporting
In either case, how the part or substrate is controlled under the print heads affects drop accuracy and registration degrading print quality by:
- Moving
- Vibrating
- Stretching
- Slipping
- Bouncing
- Accelerate/decelerate
Although speed is an important area, it is one which depends on and can be limited by the ink chemistry and/or heads chosen.
Print Heads/Fluids
As you now see there is an extensive level of homework which must be done to even begin to know what printheads will suit the project best. (And, remember, this article only covers the first layer of “bubbles.)
Specifying inkjet heads has its own immense level of detail. Inkjet head considerations include, but are not limited to:
- Jetting parameters
- Gray levels
- Resolution
- Drop size(s)
- Head Position
- Compatibility with ink
- Drive electronics
- Print width/number of heads
- Stitch strategy
- Ink supply
- RIP- driver compatibility
Integrating inkjet into another production process is quite complicated. Integrators must understand all the variables within the system itself as well as how it will perform once installed. Inkjet systems are designed for a custom process and the baseline parameters should be documented upon installation.
Once integrated into production, you may find differences in print quality as the build, substrate, production, and environment change over time. It happens. It is important to understand and identify each issue separately. Using the list mentioned earlier as a guide, you will find it is easier to identify the cause.
These differences should be addressed previous to any color management process and production. Working continuously in the field with inkjet installs, I must often apply a bit of print quality triage before the color management process can be applied, by defining and providing solutions to the issues mentioned above.
Print quality is based on the reproduction of set parameters… and color management is based on the reproducibility of print quality. The more stable the system, the more predictable your color.