The uses of inkjet have grown steadily over the last two decades, taking in 2D, 2.5D and 3D applications. The improvement in productivity throughout has been made possible by increasing levels of technical wizardry. Nowhere is this demonstrated better than for our well-known production printers, which are very, very clever boxes of tricks. For manufacturing-style applications, however, it is sometimes necessary to get back-to-basics when it comes to optimising the process. Even if it is only a single material we are planning on printing with (like a clear varnish), there are some basic principles that need to be considered. In this short series we shall look at these starting with the concept of “single-pass” printing.
The Importance of Drop Placement
Many of the new inkjets we see in offices make use of “page-wide” arrays of heads, replacing the scanning carriages of smaller machines. The principle is that every pixel row of every pixel column in the image gets printed with just one single movement of media under a nozzle. This “one-hit” approach, which has been the main way to put inkjet into serial production lines, means that it is important to consider several sources of error that are only possible to hide when taking more than one pass. Most of them involve drop to substrate accuracy for colour and print quality as well as proper jetting of coatings for protection and graphic enhancements.
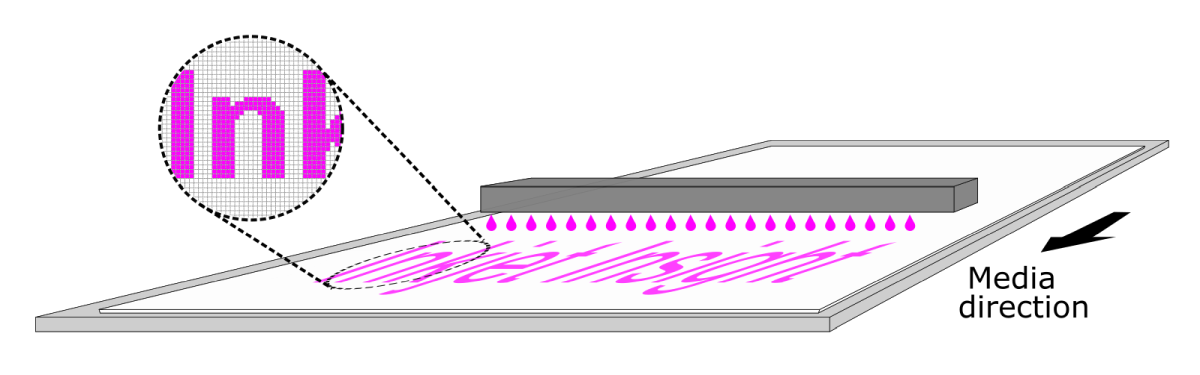
Figure 1.
The first challenge is mechanical alignment, as shown below. For most print heads offering a higher nozzle/inch ratio, the fact they are built up of multiple rows, as shown on the left-hand-side of Figure 1 above, means that rotation is important. If more than one head is used, then the accuracy of stitching the heads together is also important. The combined effect of alignment and stitching is shown schematically on the right-hand-side of Figure 2 below.
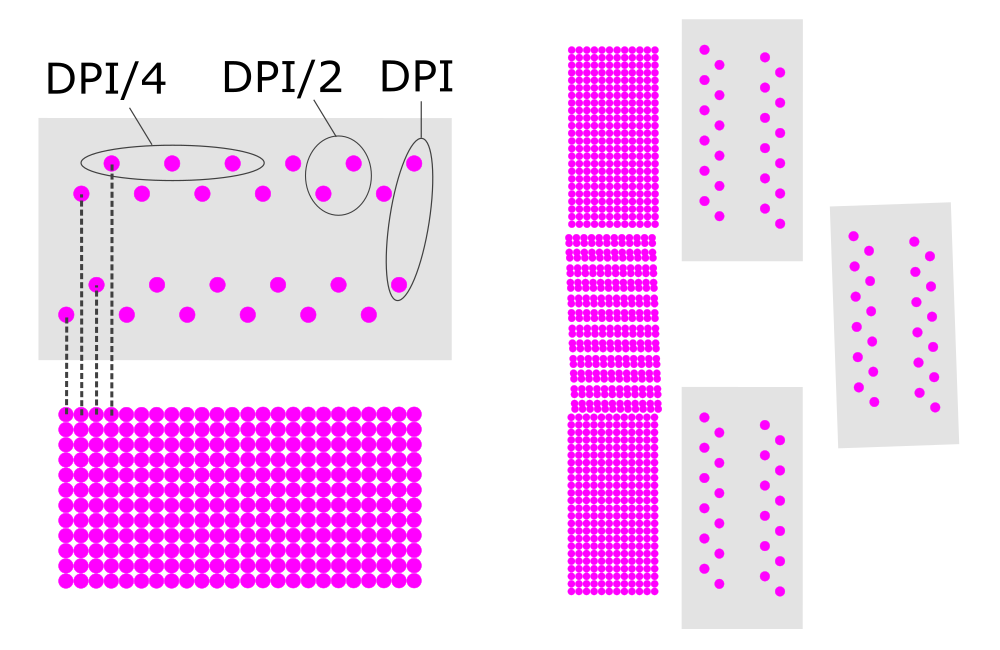
Figure 2. Importance of spacing and alignment of nozzles to drop placement
The tolerance of these mechanical considerations is very dependent on the application. For instance, one reason the ceramic tile market quickly adopted inkjet was that it was a process that was slightly more forgiving compared to printing plastic foils for labels. A bit like printing plain paper compared to coated paper.
Once the nozzle rows are spaced nice and evenly then a large part of the accuracy comes down to the timing of the jets. Again, multiple rows make single-pass printers a little more sensitive and if the speed is not measured or controlled precisely enough then “horizontal” lines are no longer straight. This is because the space between nozzle rows is set by design, and often related to a multiple of the native resolution of the head. If the substrate moves just a little bit more or less than expected, drops from one row don’t land next to those from another. The effect of alignment and timing can be seen quite clearly in the pictures below taken from a Dimatix Starfire Printhead printing at 400DPI.
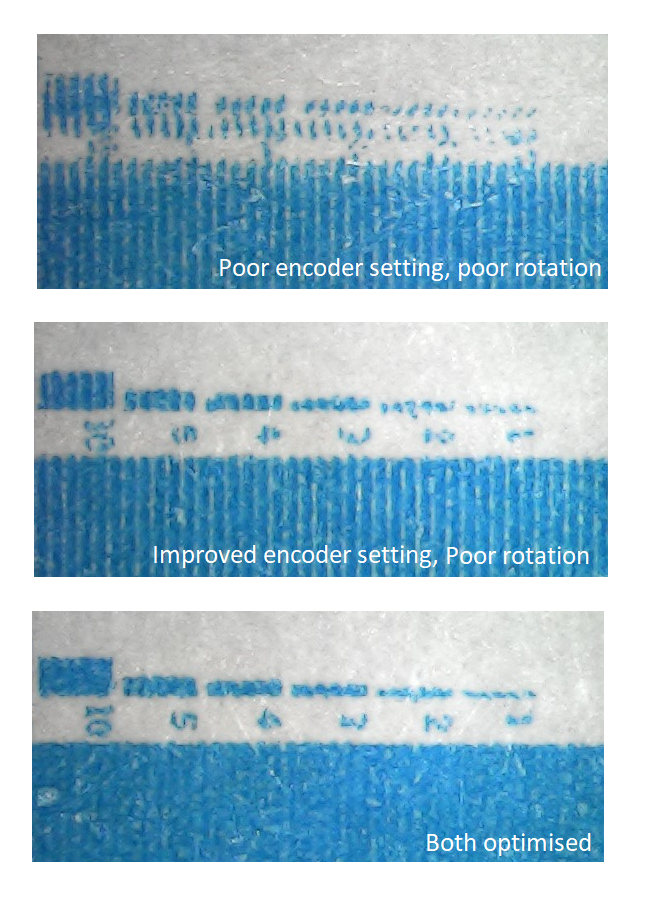
Figure 3. Alignment and timing of drops is critical for accurate drop placement
Once everything is moving correctly, then it is a simple matter of getting the right amount of ink/coating to be applied. We can do that either by controlling the pixels/inch in the process direction, or by changing the droplet volume. The first is easier to picture – more pixels = more drops = more fluid. With piezoelectric drop-on-demand heads, the other way we can control coat weight in single pass is by the use of the printhead waveform. Waveforms are electrical signals used to precisely control the amount being jetted and, just as importantly, the speed.
Factors of Drop Speed and Size
Why are droplet speed and size both important? Well, not all industrial processes are flat like a web of paper, so the drops may need to be thrown further to reach the target, meaning they are subject to air drag. The graphic below shows the effect of different waveforms in producing different drop sizes and the drop speed influence as a function of distance. You can imagine that when trying to deposit onto extruded decorative profiles, for example, that this can have large effect on being able to print the same quality everywhere.

Figure 4
When developing for manufacturing applications, the OEM must consider all these factors so that they can produce the necessary quality. It is a trade-off between the extra process steps of printing onto something that is laminated or transferred (dye-sub) or printed direct-to-shape. The challenges of the latter can sometimes mean that single-pass print head mounting arrangements can be less conventional, or that robots are sometimes used to help heads navigate non-linear paths along more complex shapes. In some recent examples in the cosmetic industry that motion control is actually from the human hand (Get Skin in the Game)
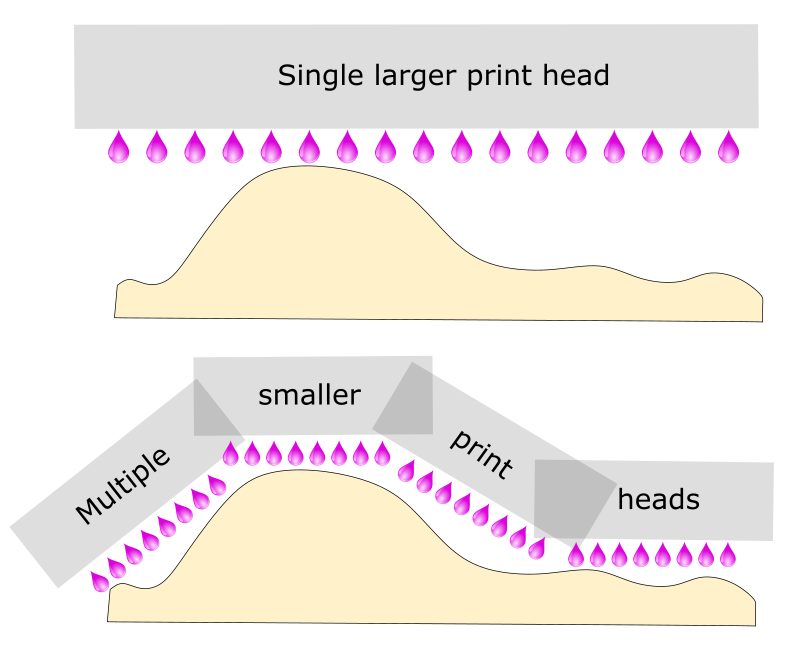
Figure 5
When integrating inkjet into your process, drop accuracy is one of the variables you will find within the development process. Drop accuracy influences print and colour quality of the printed product.
In future posts, we will expand into additional properties of ink such as viscosity and surface tension and their influence on print quality for single pass applications.