Sponsored content
Fujifilm, which has been developing inkjet integration projects for some years, is now making a more public play in this market to help customers add inkjet to their existing manufacturing processes through its FUJIFILM Integration Inkjet Solutions team. This is quite distinct from Fujifilm’s better known business in selling printing systems as well as components or sub-assemblies for OEMs looking to build their own presses.
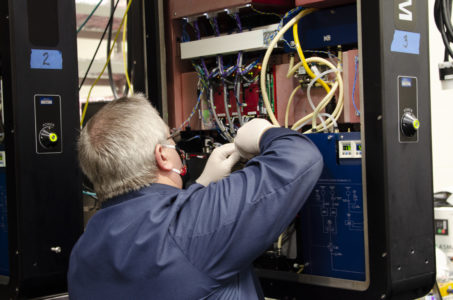
Here an engineer adjusts a Fujifilm wide printbar system.
Fujifilm’s integration business is focusing on custom configurable systems designed to address a customer’s specific requirements in a way that provides additional value compared with off-the-shelf presses. This is because an off-the-shelf printer is typically designed to be most efficient at printing a given volume and application, whereas an integration project is about meeting a client’s specific application needs, which are typically aimed at improving overall process efficiency. That might be because introducing an inkjet element allows the process to be much shorter and to take less time, or result in less waste, or it might come down to simply realising greater efficiency in the overall supply chain.
Steve Atherton, Senior Product Manager for Fujifilm Dimatix, adds: “Inkjet technology has matured in some areas to the point where long-established expectations and practices can now be questioned and can often be changed with new technology for improved efficiency. For example, how useful is it to calculate cost-per-print if there are regular periods when you cannot print due to lengthy startup routines?”
There’s a wide range of potential applications, starting with adding variable data to commercial print, such as for direct mail or transactional documents. Equally, there are various types of packaging, including corrugated, folding carton and flexible film, where the aim might be to eliminate the inventory of pre-printed material to get a faster response time to market for promotional runs. Other uses include direct-to-shape printing, such as printing directly to a bottle as part of a bottling line to eliminate the labelling stage, or other industrial printing such as construction materials or tools, or even printing edible inks directly to cookies and candies.
These kind of projects are typically carried out by small specialist companies but Atherton argues that Fujifilm can offer the kind of security these markets require as they scale from niche applications to mainstream adoption: “Fujifilm obviously brings technology like printheads, inks, and manufacturing capabilities, but the key to a successful inkjet integration business is the ability to scale technology efficiently.”
He continues: “This requires a delicate combination of engineering rigor and flexibility. You can’t afford to reengineer systems for every market, and if you could the result would be inconsistency that does not work in places where high production efficiency is critical to success such as in packaging conversion.”
Atherton points out that his team is working directly with the Fujifilm Engineers who are responsible for producing printheads and other imaging technology, adding: “So if there’s any kind of a question we can just call up the person who invented it and get an answer straightaway.”
Equally, Fujifilm Integration Inkjet Solutions can draw on a vast range of different ink technologies, which includes direct contact food inks, dye- and pigment-based aqueous inks, as well as UV-curable and even hot melt and solvent inks. Atherton adds: “With enough different types of ink in your portfolio, you can work on mastering the combination of ink, printhead, and system elements to optimize inkjet performance for a wide variety of needs. You couldn’t do that if you only had a few inks and printheads to work with but if you have enough you then have a toolbox that you can use to solve numerous problems.”
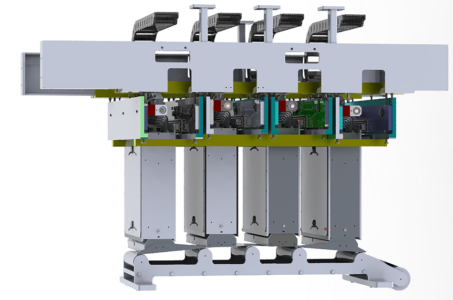
This image shows a 4-color inkjet system
However, there’s more to this service than just having good inkjet capabilities. These kind of bespoke projects also demand understanding of the various manufacturing processes that inkjet will be incorporated into. Atherton explains: “We have a lot of people who are really good at going into customer sites, understanding their existing processes, knowing what is important to understand, and then formulating their ideal printing solution, which won’t be anything you can buy in a catalog. We do that by selecting the right technology building blocks within a flexible set of inkjet printing architectures. And that is the essence of what makes us good at what we do.”
He adds: “We try to provide a holistic solution approach, where we provide the technology and work directly with the customers to get it working on their systems. You wouldn’t expect working with Fujifilm to feel like working with a small, family business, but as we’ve grown we’ve made it a priority for our team to retain the approachable culture of a small integration business.”
And the Fujifilm Integration Inkjet Solutions team has plenty of experience in doing this. Fujifilm has been offering this service for the past 15 years and has built up a considerable level of expertise. However, in the past only a select number of large customers have been able to commission a bespoke integration solution from Fujifilm.
So what has changed? Atherton explains: “We now have the kind of technical architecture and production efficiency to scale our capabilities and make them more broadly accessible. We see that there’s a lot of areas that can benefit from our capabilities in a range of industries – from packaging and decor to commercial printing – and so in order to cast such a wide net to reach these different industries we want to be a little bit more proactive in promoting our services.”