Sponsored by Contiweb
The first article in this series provided OEM and customer insights on how an auto-splicer, in-line with inkjet web presses provided significant cost benefits, reducing the time needed to change reels and releasing more saleable capacity. This approach drives further operational efficiencies because operators do not extend the downtime for reel changes to accomplish other tasks if the downtime does not exist in the first place. There are even more advantages provided to companies using continuous unwinding systems beyond the productivity benefit.
To maximise efficiencies, the non-stop unwinder should be integrated into the press line to handle the necessary actions at a reel change. This will include stopping print before the join, identifying and removing the splice and restarting printing to avoid losing any content. A splice comprises the old reel, the double sided tape and the new reel creating a thicker area on the web that passes through the press. The print gap between the nozzle plate of the inkjet head and paper surface is around 0.5mm on piezo presses, and the higher thickness of the splice could come into contact with a head unless the heads can be moved out of danger. This can be done in a manual change after the press stops, but it wastes a lot of time and paper before the press restarts. Fortunately, automated solutions are available to handle reel changes.
HP talks about “Jumping the splice,” an automatic routine that lifts the heads on their PageWide Web Presses, lets the splice pass the printheads safely with a non-printed frame that is sized appropriately for the speed of the press, and the press is back into production with zero content needing to be reprinted. The amount of waste can be defined by the customer, the operation takes less than three seconds and with integrated finishing, the splice is automatically removed without stopping. Kodak offers a similar solution on its Prosper machines. The customer can set the parameters for each change to make it easy to remove at the finishing stage. Many piezo presses do not have this capability (yet). This is one reason for relatively low uptake among piezo press owners, because to effect a repair if the heads are damaged is both expensive and time consuming. As their performance is proven, more manufacturers will integrate the automated handling of splices. Some Canon, Screen and Ricoh customers have done custom implementations with their OEM in order to run auto-splicing.
An implementation challenge for some of the older inkjet presses is that the machines will run a clean/purge cycle to refresh heads at a roll change. As ink performance in the heads has improved this need for purging falls, making the use of auto-splicing more attractive. Of course, it is not just the unwinding at the front end that may be needed. To get the maximum benefits of eliminating downtime, the print company needs to automate handling the printed reels at the back end. It is easier to change a rewinder than the unwinder. The operator just removes the reel, loads a new core, tapes the end and the press is ready. Usually the reel change includes removing the printed reel unless the press has an integrated finishing system, increasingly common in books, newspapers and commercial print where sheeters allow continuous running. These finishing systems will usually identify and remove the splice while maintaining continuity of the print run.
Most mailing systems process printed reels and Contiweb offers the CR-N rewinder for non-stop running. When it is time to change the reel, the festoon takes up the print while the rewinder halts the full reel, cuts the paper and splices the web to the empty reel. The paper in the festoon then feeds onto the new reel. In commercial print operations, as well as books there will be a range of papers in use and partial reels are common. Auto-splicing potentially allows companies to batch files together and automatically switch reels when the paper changes without stopping. However, changing paper types involves changing the running properties, different web width, calliper and potentially a new paper surface requiring a fresh colour calibration. Storing the settings as a recipe allows the press to automatically make the adjustments as the paper changes, calling up the recipe to avoid stopping for manual calibration.
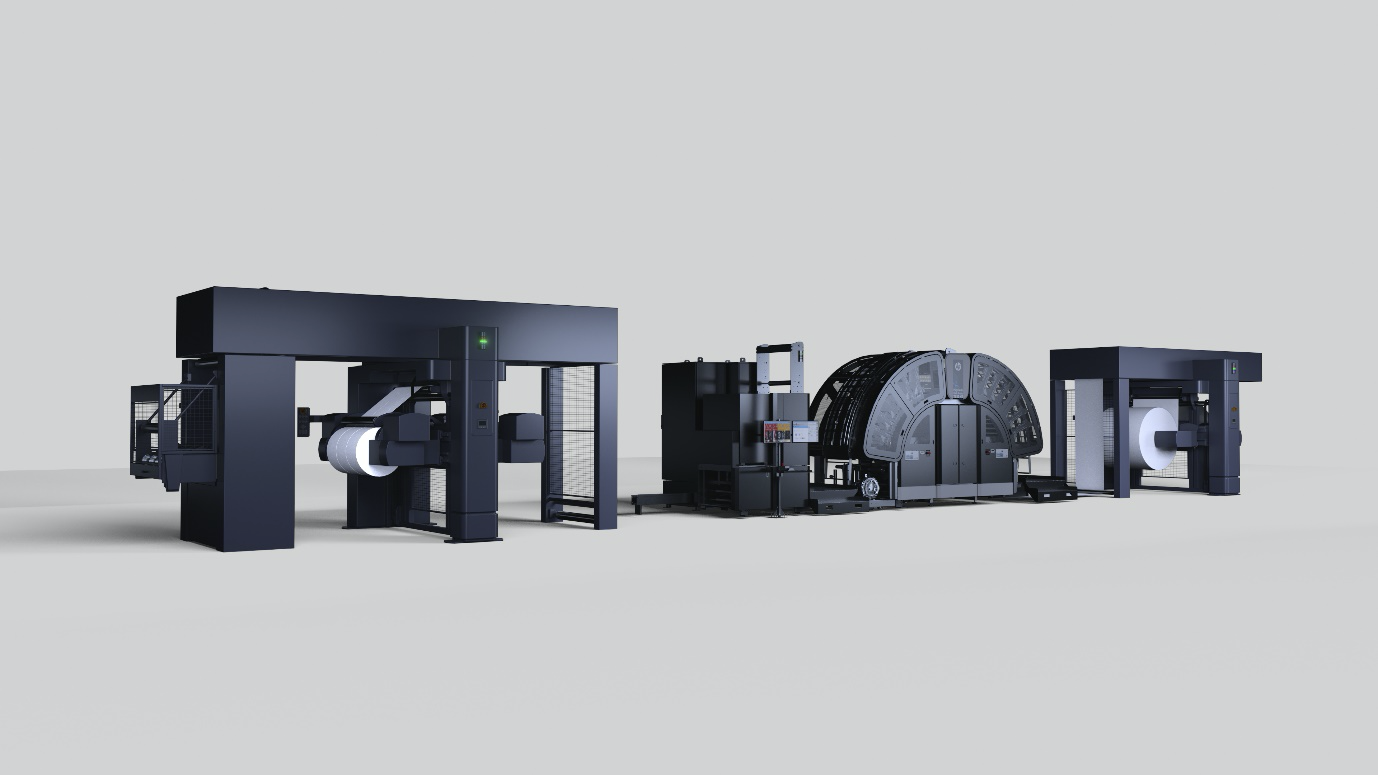
Contiweb CD-N non-stop unwinder and CR-N auto rewinder on HP PageWide T250HD inkjet press
Press operators are generally very enthusiastic about auto-splicing as part of their routines. There is less manual lifting and removing a laborious, repetitive task releases time for the operators to attend to other tasks. It could be preparing paper and files for the next job, arranging to do some calibrations on new papers or clean up the digital front end. It can make the job description more attractive to interest new, high-skilled people. It can also enable facilities to have operators running multiple press lines which is hugely beneficial as labor markets tighten. For some plants an advantage may be in down-skilling the operator requirements to allow new hires to run the equipment. The auto-splicers deliver consistent joins that work well, avoiding fails and breaks. It can help both highly skilled operators and new starts with no experience. This improvement in consistency compared with manual changing leads to less slab and core waste. In 2022 reducing paper waste is even more important as printflation has increased paper prices and some companies report supply shortages. As companies look to minimise waste and do more with existing kit, the current supply chain issues are encouraging printers to maximise the performance of existing assets. Auto-splicing offers sustainability benefits that customers and more importantly end users demand. As Kristin Albee of HP comments, “People and paper are precious”.
The other significant benefit that users report for the Contiweb system is that it can boost quality at high press speeds. The Contiweb CD-N is a horizontal, zero-speed compensator splicer with fully automatic splicing and integrated infeed. The high-specification festoon and guide rollers maintain optimum web tension control. This continuous infeed helps control the web tension resulting in quality improvements with inter-color and back-to-back registration. Matt Baldwin, VP Operations at CPI, one of Europe’s biggest book printers, says, “We see significant quality improvements through the improved control of web tension resulting in better quality, delivering even sharper text on mono presses. This is important on inkjet machines running at 305m per minute.” As the top speed of other presses increases and print companies use inkjet for more applications this will be very useful.
Press manufacturers usually offer a free choice of the reel handling system to their customers to meet their individual preferences. The selling and support is a single contact point. Uptake of automatic high speed splicers will grow over the next few years as printers look to improve productivity, get more from press operators and offer improved levels of quality. As faster presses come to market, such as Kodak’s Prosper 7000 with a top speed of 1,345fpm (410m per minute), the need for automating reel changes is even more important. There is also a significant sustainability advantage which is increasingly important in 2022 and beyond.