Few markets have sparked the interest as much as corrugated printing with inkjet. Several inkjet presses have either been announced or are already available. The Kento Hybrid brings a new twist to it.
Kento Digital Printing is a new company founded by several veterans with corrugated printing, inkjet technology, and industrial manufacturing backgrounds. From his experience in the corrugated packaging industry, Kento’s CEO Javier Quesada had the idea for a hybrid inkjet press to bridge the gap between analog and pure inkjet printing. Founded about three years ago the company secured financial backing and formed a partnership with Cellmacch. Today Kento has 32 employees and keeps on adding staff.
Press Specifics
The Kento Hybrid press features a print format of 2.1 metre width and 1.3 metre length. Sheets are fed long edge first as in conventional presses, allowing for a more compact press design as well. After feeding, the sheets are printed in one or multiple conventional flexo units followed by an IR and hot air drier. Afterward, a primer unit prepares the sheet for inkjet printing, especially when using coated substrates. The press uses Seiko inkjet heads with a resolution of 360 dpi and 4 grey levels and prints in CMYK with UV inks. A patented automatic registering system for flexo to inkjet register is integrated. After inkjet printing a flood overprint varnish can be added. Beyond offering protection of the image the varnish can reduce gloss differentials between the UV ink and the flexo print, if that is desired.
Print speed is up to 80 m/minute or 9,000 sheets/hour. All types of corrugated substrates are supported, up to a calliper of 12 mm. Kento points out that all components are driven by the same (Siemens) technology, which allows for better coordination of the modules.
The sheet transport and analog printing units have been designed and are manufactured by Celmacch from Italy. Celmacch is a leading manufacturer of sheet-fed flexo corrugated presses with more than 30 years of history. Since Koenig & Bauer acquired a stake in the company in 2022 the company has been renamed to Koenig & Bauer Celmacch. As in conventional presses, the number of flexo units is not limited, although Javier reckons that two units would be the preferred solution. With two units two different anilox set-ups would be available for a quick ink volume switch.
Kento does supply the inkjet imaging unit, the front end and provides support and service. A service team in Europe is already established, while the US team is being built up currently. Kento realises that service is critical and offers 24×7 support and a mix of onsite and virtual assistance. A direct sales office for the US has been established while in Europe agents will take on sales in the different countries.
Kento does not sell ink and users are free to buy inks from their manufacturers of choice as long as they are certified by Kento. Kento plans to certify food-compliant UV inks only. So far two ink sets have been certified with a third to follow soon. Kento is also working on a press version with aqueous inks.
Plans for an inline rotary die-cutter and a reverse side printing unit exist. A first installation with an inline die-cutter is envisaged for end of next year. A reverse printing unit will be on offer at a later stage.
The Hybrid Approach
The Kento Hybrid is aiming at run lengths where pure inkjet and analogue print overlap and neither technology is very efficient. With increasing run lengths inkjet inks become quite expensive while setting up a process colour analog press is time-consuming and costly.
The idea is to use the flexo unit on the Kento Hybrid for high ink load areas, especially spot colours without requiring process colour separations. Inkjet is used for the full colour graphics and variable content. Ideal would be versioning where the flexo portion is used for multiple runs and the process colour graphics portion is changing. According to the manufacturer, the sweet spot of the Kento Hybrid is between 1.500 m² and 5.000 m².
An interesting option is to preprint white using the flexo unit, which would allow printing full colour inkjet graphics on brown/kraft substrates without requiring expensive white inkjet ink. Also, the flexo unit could be used for specialty inks like metallics. Another advantage of the flexo unit(s) is that spot or brand colours can be printed, relieving the need for an extended gamut of the inkjet unit beyond CMYK.
A first line has been installed at Grupo La Plana near Valencia in Spain, a major corrugated packaging manufacturer in Spain. The press has been installed in March 2022 and is producing box and display jobs for a wide range of customers. The second installation will head to the US shortly, to be installed in January. Both sites will double as demo machines while running customer jobs. A third line for the US has been ordered already.
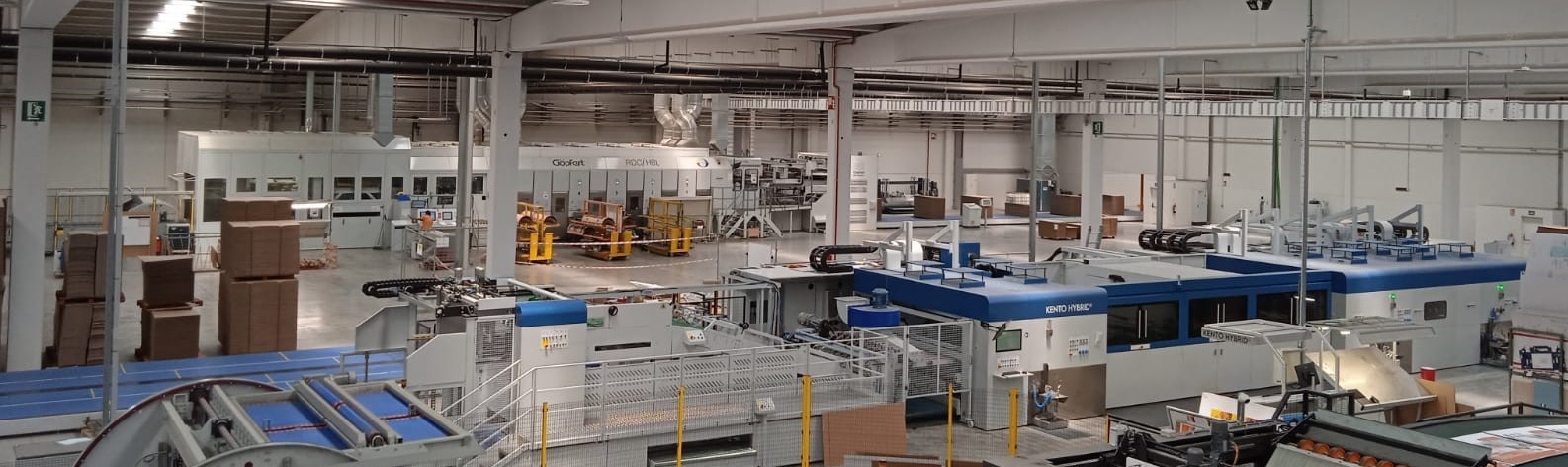
Kento Hybrid at Grupa La Plana
Who Would Benefit
The Kento Hybrid addresses so far a unique portion of the postprint corrugated market with the idea to offload the heavy coverage portions of an image to flexo with its lower ink cost. Another unique feature is being able to run spot and specialty colours, which is not possible with inkjet so far.
As a downside, the press requires making a flexo plate(s) and ensuing set-up times, which need to be amortised with sufficiently long runs. Kento cites about 10 minutes for a plate and ink change. Set-up and start-up waste should be fairly efficient as simple spot colour graphics do not require a lot of registering. With the cost of inkjet ink at 35€/kg and for flexo ink of 5€/kg Kento has sample calculations resulting in ink costs of €65 to €134 per 1000 m² using the hybrid approach, compared to around €300 for pure inkjet. These savings would need to counterbalance the costs for a flexo plate, the change-over, ink mixing and other flexo-related costs.
How much sense this approach makes will depend on what work is typically being printed, especially whether jobs typically include large, dark solids. It will also depend on the typical print runs, as setting up the flexo unit makes the most sense for medium runs – although the Kento Hybrid could print in digital-only mode for very short runs.
Inkjet installations today often struggle to get enough short-run jobs to make good use of the press. The Kento Hybrid should be able to extend this window into higher runs. Other current inkjet users in corrugated move to display work, often replacing litho laminate. For the Kento Hybrid with its lower resolution of the Kento Hybrid, this is less of an option.
Of course, for a start-up company like Kento manufacturing a massive press (and investment) all eyes will be on the first installations, how they perform and are supported. It will be very interesting to get user feedback in the future and how the press is being used.