I have written many articles about Landa Nanography since 2012 when it was first introduced. In this article I will give you an update; however, if you follow the links in this article you will get an in-depth look at the history, company, and technology.
This new technology created significant industry buzz based on the promise of an offset quality B1 sheetfed inkjet press that would operate at 13,000 sheets per hour. When drupa 2016 rolled around, customers were anxious to buy one and take it home. Although, while the products and story were filled in with some more detail, it was still not ready for production release. In 2017, I had an opportunity to tour the factory and visit the first Landa beta site: Graphica Bezalle in Israel, not far from the Landa factory. Graphica Bezalle is a packaging printer that installed a Landa S10 simplex press. I was impressed with the evolution of the technology and the resultant quality I saw, although it was evident that there was still some work to do. They talked about some other beta sites on the horizon, but after that they went into a self-imposed quiet period.
Building Out the Company
Well, they may have been quiet, but they have also been very busy. And now they are ready to start talking. I recently visited their first S10P duplex press beta site, Mercury Printing in Rochester, N.Y., along with a small cadre of analysts and press. Nachum Korman, VP & GM Americas for Landa Digital Printing, gave us a fairly detailed overview of what they have been up to recently.
First, let’s talk about global installations. Currently, they have three S10 (simplex) presses installed, with another five S10 presses set for installation before the end of the year. They have one S10P (duplex) press installed with another three S10P presses set for installation before the end of the year. They will be installing their first web press, the W10 simplex, before the end of the year as well. That should give them about 13 installed presses by the end of the year, with drupa 2020 coming up.
When I was Israel in 2017, they had two manufacturing facilities. Landa has been ramping up production to help meet demand and now has three manufacturing plants operating with a fourth significantly larger plant going on line shortly. One of those smaller plants (#3) is dedicated to ink and consumables production. In order to support the current and future installed base, they have been building global and regional organizations as well. In the Americas region, there is a new headquarters in Alpharetta (Atlanta), Ga., also the US home of Heidelberg and regional headquarters for HP, so they have some neighbors. Operating out of the Atlanta HQ, they have operations, sales, application, and technical support. They are placing service engineers geographically near the press installations to work with the customers and also give feedback to the manufacturing engineers. Currently, there is one located in Rochester, N.Y., and another one will come on line in Texas to cover the S10 installation at Virtual Packaging in the Dallas area.
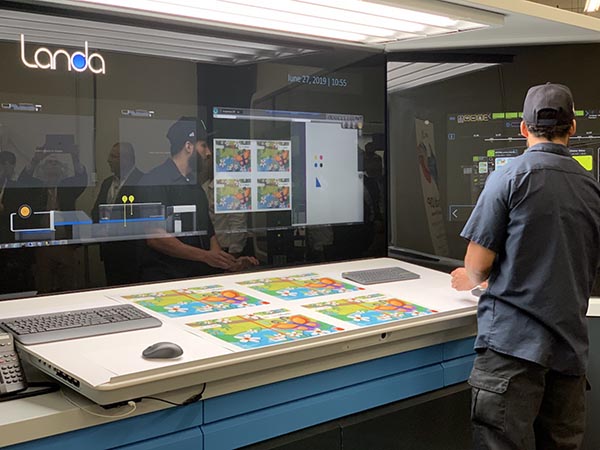
Landa Cockpit
As the installed base grows, they expect to increase the support staffing within each of the regions. For customers who purchase a press, in preparation for installations, there is a 12-session online training course followed by one week of training in Israel at the customer experience center. To ensure a smooth press installation, one of the members of the team that built the press oversees the installation of that same press at the customer site. The regional support is the first line; however, they also have implemented a global service center in Israel that operates 24/7.
In order to ensure ink, consumable, and parts availability, they have selected UPS as their logistics partner. Through this arrangement, they will be able to maintain national and regional supply availability near the machine installations. The global service and support facility is in place in Israel to offer top tier support to the regional teams.
Update on Quality and Technology
While my previous articles (see links above) covered the core Landa technology and expectations, I thought it was time for an update and to fill in some gaps now that there are production presses in the field.
In the past, I have discussed AQM (Automated Quality Management), the technology Landa uses to manage and control many of the system operations in the presses. AQM really addresses a lot of what in offset and some digital presses occurs with hardware, but in Landa presses it is largely software. AQM manages registration control as well as full sheet visual inspection. If a sheet fails inspection, it is ejected. However, there are many other things in the works for AQM, and Landa currently does a regular software update release about every three months, so the press operation and quality are constantly improving.
While initially there were promises of an optional run speed of up to 13,000 sph (sheets per hour), the press currently operates at a fixed 6,500 sph, which is the standard speed that was promised. Even at 6,500 sph, it is significantly faster than any of the other comparable cut-sheet production inkjet presses. For example, the Heidelberg Primefire 106, a B1 press, is currently operating at 2,500 sph, and the updated Fujifilm J Press 750S, a B2+ press, currently operates at 3,600 sph. Interestingly, all of these use imaging units with Dimatix Samba printheads. Each of the press manufacturers expect to offer speed upgrades in the future, although the Landa process is currently the only one that can address the problems related to airflow created between the moving media and the printheads. Landa is expected to introduce a higher speed option at drupa, but there is currently no indication of what that will be.
Landa image quality and media range are due to the advantage of impressing ink (dry polymer) on the media from the blanket after almost all of the liquid has been evacuated. This allows almost any media to be printed without any pretreatment. In the example below you can see a photo I took of gloss and tissue paper, both very impressive, and as a result of the firm shaped ink dots, even the flesh highlights are very smooth.

Gloss coated (left) and tissue paper (right).
I had a chance to look closely at the blanket that offsets the ink onto the media. The back side is composed of a micromesh that gives it stability and facilitates heat distribution to evacuate water in the ink. The surface is a very smooth polymer which receives the ink from the printheads and then releases it onto the media after it has evacuated liquid.
While Landa and the customers are still trying to figure out how long a blanket will last in production, they are recommending that it be changed every two weeks. Once the customers and Landa have had some time to truly test the effective life of the blanket, they can adjust the recommendation based on impressions and media type (coarse vs. smooth), all of which will have impact on blanket life. The process of changing the blanket takes about 1½ hours, and according to Mercury is a fairly straightforward process.
Application and Use
Mercury is a very impressive company with a long history of offset and digital printing experience. They do a lot of educational and book work as well as an assortment of commercial work. In speaking with both CEO John Place and Director of Process Development Felix Medero, this press has been fantastic. Quality is not the determining factor for placing work on the Landa vs. the offset presses. In fact, they say the Landa quality is better than offset. As it stands today, anything that needs collation is run on the press since they have found that the cost and time savings are significant running it on the Landa. It is running all the time, and the biggest issue seems to be what work not to run on it. It is a very productive machine. In fact, in the approximately 45 minutes we were in the pressroom looking and the machine and even stopping it for us to take pictures of the inside, they ran nine different jobs.
From what I can gather, it has been worth the wait, and we can only expect more presses to be installed and things to keep getting better.
More to Come …
I would like to address your interests and concerns in future articles as it relates to the manufacturing of Print, Packaging and Labels, and how, if at all, it drives future workflows including ‘Industry 4.0’. If you have any interesting examples of hybrid and bespoke manufacturing, I am very anxious to hear about them. Please feel free to contact me at david@zwang.com with any questions, suggestions or examples of interesting applications.